Learn about Different Types of Milling Cutters for Improved Productivity
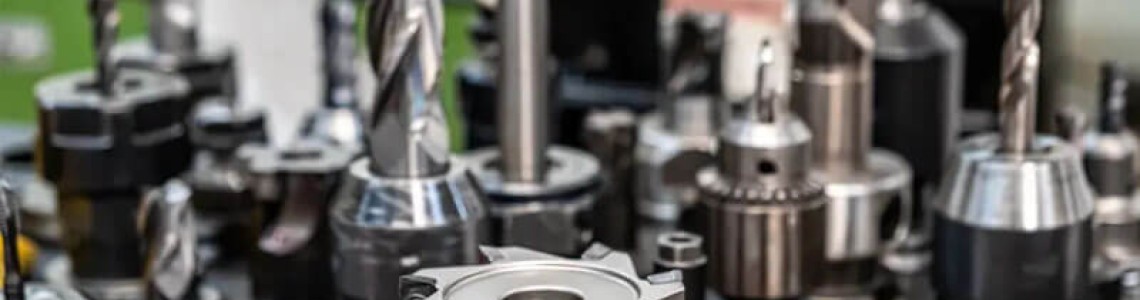
Milling cutters are specialized tools used in machining and have different shapes and sizes to suit different materials and applications. Knowing the differences between these cutters can help you get better results with your projects.
1. What Are Milling Cutters?
Milling cutters are widely used for a variety of machining operations. They come in a wide range of sizes and shapes and are used to remove material from a workpiece by cutting or grinding away at the material. Milling cutters can be made from durable materials such as high-speed steel, tungsten carbide, and cobalt alloys, making them suitable for use in a variety of industrial applications.
These tools are used for various operations such as contouring cutting grooving or shaping metals depending on the type of cutter used. With the right combination of cutting tools and machining techniques, it is possible to create precision parts with incredible precision and accuracy. The flexibility of milling cutters makes them a must-have tool for any machine shop or metalworking facility.
2. Different Types of Milling Cutters
There are several different types of milling cutters available, each designed for specific operations such as face milling, end milling, shell milling, and more. To maximize the performance of your machining process, it is important to choose the right cutter for your specific needs.
The most common milling cutters include:
● End mill
● Face mill
● Ball cutter
● Slab mill
● Side-and-face cutter
● Involute gear cutter
● Fly cutter
● Hollow mill
● Shell mill
● Roughing end mill
● Dovetail cutter
● Wood ruff cutter
● Thread mill
Each milling tool has its own unique features and performance capabilities. Some are designed for greater precision and accuracy, while others can handle tougher materials or larger objects. Understanding the different milling tools available, their features, and their performance is key to making the right choice when it comes to your projects.
● End mill
An end mill is a type of cutting tool used in machining. It is designed to cut materials such as metals, plastics, and wood at high speeds. End mills feature cutting edges on the end and sides of their cylindrical bodies which allow them to create complex shapes and contours quickly and efficiently.
End mills are a type of tool commonly used in machining operations. They have a flat bottom, but there are also versions with round and radiused edges. End mills differ from drills in the sense that they can make lateral cuts along the material, which is an advantage for milling operations.
● Face mill
A face mill is a type of machining tool used to remove material from the surface of a workpiece. It features several cutting edges that rotate around its axis, which allows it to cut quickly and accurately. Face mills can be used on many types of materials such as aluminum, steel, and titanium, making them an essential tool for any machinist's arsenal.
Face mills are cutting tools used for milling operations that make use of carbide inserts. Unlike other milling operations, these tools cannot cut axially. Cutting edges are found on the sides of its head, making them easy to replace with new carbide inserts which improve the lifetime of such a tool while still providing excellent cutting quality.
● Ball cutter
A ball cutter, also known as ball mill, is used for cutting materials. The hemispherical cutting tips of these tools are designed to create a corner radius for perpendicular faces.
It's used to precisely cut round objects such as golf balls, bearings and other similar materials. It is typically composed of two parts: the cutting blade and the holding fixture. The cutting blade must be sharp enough to pierce through the object being cut, while the holder keeps it in place for a secure cut. Ball cutters are useful for drilling holes in rounds objects so that they can be mounted on fixtures or machinery for further processing.
● Slab mill
A slab mill is a type of grinding machine used in metalworking to shape large pieces of metal into flat, thin sheets. It is usually used for grinding thick pieces of metal, such as steel and aluminum. This process helps to create precise dimensions and smooth surfaces. Slab mills are an essential tool for machinists and metalworking professionals due to their versatility and ability to produce high-quality work.
Slab milling is an effective and efficient method of machining large surfaces on manual milling machines. The slab is held in a horizontal position between the spindle and the support, and then it spins to quickly machine the surface. This technique is also sometimes referred to as surface milling due its impressive results.
● Side-and-face cutter
A side-and-face cutter is a powerful and versatile machine tool that is designed for cutting and shaping metal components. It features a rotating cutting tool that is capable of producing intricate and precise shapes in a variety of metals. With its advanced design, the side-and-face cutter can be used to create objects with complex curves, intricate profiles, and unique geometries. It is an essential tool for the production of high-quality parts and components.
Before the advent of the end mill, side-and-face cutters were widely popular due to their design. They featured teeth around their circumference as well as along one side, making them similar to modern end mills. However technological advancements have since caused them to become less popular.
● Involute gear cutter
Milling involute gears requires a special cutting tool, as there are a range of different cutters available suited for producing gears within the certain number of teeth.
An involute gear cutter is a tool used in the manufacturing of gears. It is designed to cut gear teeth along an involute curve. The involute helps ensure each tooth on a gear engages properly with its counterparts, providing smooth and stable operation when the gears are paired together. Involute gear cutters are vital for the precision manufacturing of high-quality gears and components.
● Fly cutter
A fly cutter is a type of milling machine that uses a single cutting tool to produce multiple cut surfaces in the same pass. This method offers an efficient and cost-effective way to create components with accurate shapes, sizes, and depths. The fly cutter is particularly useful for bringing complex parts into shape quickly, allowing for mass production without any loss in quality.
Fly cutters are tools that have a similar function as face mills, with a central body that holds either one or two tool bits (double-end fly cutters). Though they are a cheaper option, their cutting is not as high-quality as face mills. Plus, the machinist can often make the cutting bits in their shop instead of buying them from stores.
● Hollow mill
Hollow mills are versatile tools for milling operations. They have a hollow center, which allows them to perform a range of operations, including drilling, reaming, countersinking and more. The hollow head design enables users to work in tight spaces around obstructions such as walls or other components. Hollow mills are designed with a variety of cutting edges to accommodate different materials and applications.
Unlike face mills, hollow mills are used to achieve a cylindrical outcome by feeding the workpiece into the inner part of the mill.
● Shell mill
A shell mill is a type of rotary cutting tool that uses multiple cutting edges, arranged in a spiral pattern, to cut away material. It is frequently used for high precision machining and can handle most materials with ease. The multiple edges allow for faster cuts and less strain on the machinery being used than with other types of tools. Shell mills are especially useful in applications where there is limited access or space to make traditional cuts.
Shell mill is typically used to cut grooves and other shapes into the face of a workpiece. It gets its name from the fact that it resembles a shell shape when it is viewed from the side. Shell mills are often made out of high-speed steel or carbide, allowing them to withstand high temperatures and pressures while cutting through tough materials.
● Roughing end mill
A roughing end mill is a type of tool used in CNC machining that is designed to remove large amounts of material quickly and efficiently. It has a larger cutting diameter than typical end mills, allowing it to quickly cut through thick and hard materials with ease. This makes it ideal for creating precision parts in a short amount of time.
Roughing end mills utilize cutting teeth with a jagged edge, which helps to cut through workpieces faster than conventional end mills. The smaller pieces of metal that are created from the cutting process can be easily removed from the workpiece. Additionally, multiple teeth come into contact with the workpiece simultaneously during the cutting process. This reduces chatter and vibration, making it an ideal tool for certain applications.
● Dovetail cutter
A dovetail cutter is a specialized cutting tool that is designed to create intricate shapes and patterns in wood, or create intricate joint patterns in woodworking. It features sharp teeth on the blade which allows it to create clean, precise cuts with ease. This type of cutter can be extremely useful for creating furniture, cabinetry, sculptures and more with perfect accuracy.
The cutter uses a pointed bit that moves along in a sawing motion, creating the familiar dovetailed pattern with each pass. Its sharpened sides create a smooth, even cut with an attractive patterned groove in the middle. This particular type of cutter is most commonly used by carpenters, joiners, and cabinet makers for creating dovetail joints for furniture construction.
● Wood ruff cutter
Woodruff keyseat/keyway cutters are cutting tools used to create keyslots into parts such as shafts. The teeth of the tool are perpendicular to the outside diameter, allowing for accurate slots for woodruff keys to be produced.
The Wood ruff cutters are used in carpentry and joinery to cut grooves in wood. These grooves are used to join two pieces of wood together, making a stronger and more durable joint. Wood ruff cutters come in a variety of sizes, shapes and styles, making them the perfect tool for any project requiring the joining of two pieces of wood.
● Thread mill
Thread milling is an efficient way to produce threads without having to use single-point cutting tools. It uses a rotating tool, usually in the form of an end mill, that moves along multiple axes in order to create the desired thread shape on a workpiece. The helical flutes of the end mill help to create precise and accurate threads with great accuracy and repeatability. Thread milling can be used for both internal and external threads, as well as on small and large diameters, making it a versatile machining process.
3. How to Select the Right Type of Milling Cutter for Your Needs?
Selecting the right type of milling cutter for your project needs is an important step in achieving the desired result. There are a variety of milling cutters available that can be used to perform different operations such as cutting, boring and facing. Each cutter has its own unique set of characteristics that make it better suited for certain tasks.
Before choosing a milling cutter, we recommend that you follow our guide. Choosing the right manufacturing method or tool is a delicate balancing act between cost, speed, and quality. The cost is determined by the price of the tool, wear due to machining, and how long it takes to produce parts.
We will provide you with helpful information on what to look for when selecting the right milling cutter for your project.
- Consider the material: Different types of milling cutters are designed for specific materials.
A variety of machine tools are available on the market for different purposes, and there is also a wide selection of materials used to create them. The most common types are:
● Carbon Steel
Carbon steel is the cheapest option among all metals used for making tools and machines. Despite this, it is not very durable and can only be used at lower speeds as it loses its hardness at 200° C. This keeps the heating effect low while operating.
● High-speed steel
High-speed steel is a grade of tool steels that has been alloyed with a few elements to provide better resistance to heat and wear than regular carbon steel. This grade of tooling can provide longer life cycles, but at an increased cost. It loses its hardness at 600° C, so it can be used at higher milling speeds than other tool steels.
● Cemented carbides
Cemented carbides are a hard material and ideal for protection against wear. Although its hardness is admirable, it unfortunately has low toughness levels which can make it more prone to cracking and chipping when put under high temperatures of up to 900° C.
● Cutting ceramic
Ceramics are harder than cemented carbides and are used to produce cutting tools; however, they lack in toughness. Aluminium oxide and Silicon nitride are often used as material for ceramic tools and have different properties. Unfortunately, these ceramic tools have a tendency to crack when machining hard materials or with high temperatures - thus making them unfit for steels. In other cases, the tool life will be comparatively short.
Regular carbon steels are not suitable for most jobs due to their limited capabilities, so HSS (high-speed steel) is usually the least expensive option. However, its rate of wear means that it may not be the best choice in the long run.
Cobalt-bearing High Speed Steel (HSS) is a great choice for quick milling operations, making it ideal for most milling jobs. Cemented carbide also offers high performance milling.. However, the up-front cost may be higher, but this can result in more cost-efficiency in the long run.
- Consider the Coating: better coating increases tools' wear resistance and surface hardness
Today, most carbide tool cutting edges are coated to help increase their wear resistance and surface hardness. The ultra-smooth coating improves chip removal, reducing weld buildup and the formation of built-up edges. It also has an insulating effect to further increase the elevated-temperature hardness. Overall, these layers can result in substantially longer tool lives.
Coatings can provide a chemical and thermal barrier on tools, which reduces wear on the workpiece while also preventing diffusion and chemical reactions. These coatings have a high surface hardness, great wear resistance, stable chemical resistance, heat resistance and low coefficients of friction. As a result of these properties, cutting life is increased by 3 to 5 times compared to uncoated tools. Additionally, speed is increased by 20-70%, machining accuracy improves 0.5-1 grades and tool consumption costs is reduced by 20% to 50%.
There are two common methods used to coat surfaces: PVD coating (Physical Vapour Deposition) and CVD coating (Chemical Vapour Deposition). Both techniques involve depositing a material onto a surface to provide protection or add new properties.
CVD coatings
CVD coating utilizes materials like TiC, TiCN, TiN and aluminium oxide (Al203) to achieve a durable finish. Different PVD variants allow for refining of metals such as carbon and also other metallic elements.
TiCN: Titanium carbon nitride coating
● Depending on the application, up to four to five times longer tool life
● Very high degree of hardness and at the same time good level of toughness
● Chemical compound of titanium, carbon and nitrogen
● Nano hardness: up to 32 GPa
● Layer thickness: 1-4 μm
● Friction coefficient: 0.2 μ
● Application temperature: 400 °C
● Application: Steel (N/mm²) < 1.300, stainless steel
● Cooling is required for higher cutting speeds
TiCN coating with the addition of carbon element increases the hardness of the tool and provides better lubricity for a smooth surface finish. This makes it an ideal choice for high speed steel (HSS) tools.
TiN: titanium nitride coating
● Most widely used standard coating and universal application
● Chemical compound of titanium and nitrogen
● Nano hardness: up to 24 gigapascal (GPa)
● Layer thickness: 1-7 μm
● Friction coefficient: 0.55 μ
● Application temperature: 600 °C
● Application: Steel (N/mm²) < 900, brass and cast iron
● In aluminium, only with stationary machine tools and forced liquid cooling
● Cooling is recommended
● Three to four times longer tool life compared with uncoated tools
These coatings for HSS tools and forming tools can be applied to great effect, making them more effective in carrying out their intended purpose.
TiAlN: titanium aluminium nitride coating
● All-round coating
● Depending on the application, up to ten times longer tool life
● High degree of elevated-temperature hardness and oxidation resistance
● High cutting speed
● Chemical compound of titanium, aluminium and nitrogen
● Nano hardness: up to 35 gigapascal (GPa)
● Layer thickness: 1-4 μm
● Friction coefficient: 0.5 μ
● Application temperature: 800 °C
● Application: Steel (N/mm²) < 1.100, stainless steel, titanium alloys, cast iron, aluminium, brass, bronze and plastic
● Cooling not essential
AlTiN: aluminium titanium nitride coating
● Depending on the application, up to fourteen times longer tool life
● Very high degree of elevated-temperature hardness and oxidation resistance
● Chemical compound of aluminium, titanium and nitrogen
● Nano hardness: up to 38 gigapascal (GPa)
● Layer thickness: 1-4 μm
● Friction coefficient: 0.7 μ
● Application temperature: 900 °C
● Application: Steel (N/mm²) < 1.300, stainless steel
● Cooling not essential
Cemented carbide tools are mainly used for dry or semi-dry cutting, and their machining life can be improved by coating them with TiAlN/AlTiN. The aluminium oxide layer formed in the coating increases its hardness, making it suitable for high speed machining. Depending on the ratio of aluminium to titanium in the coating, AlTiN coatings can provide a greater surface hardness than TiAlN coatings.
Meanwhile, there are Chromium nitride (CrN) coatings and Diamond coatings. Chromium nitride coatings, or CrN, are an innovative tool coating that provides good anti-adhesion properties. This coating is almost invisible and is the preferred choice for machining operations that are prone to chip build up. It not only increases the performance of high-speed steel tools and carbide end mills but also helps improve profile cutting tools.
CVD diamond coating provides excellent durability and performance when machining tools for non-ferrous materials. It is the perfect solution for machining graphite, metal matrix composites (MMC) and high silicon aluminium alloys, as well as many other abrasive materials.
PVD coatings
PVD coatings are a type of protective coating that is applied to metals in order to protect the surface from wear and corrosion. PVD coatings are commonly used on items such as watches and jewelry, as well as industrial components, for added durability and aesthetic appeal. The PVD coating process involves vaporizing a material under vacuum onto the surface of the object in question, creating a highly durable layer that will last for many years.
PVD properties
● High purity of coatings
● Low thermal substrate impact – toughness is preserved
● Any coating materials
● Low layer thickness tolerance
● Exceptional adhesive strength (including across additional intermediate layers)
● Comparatively small layer thicknesses
For applications such as solid carbide milling cutters, drills, grooving and thread cutting or milling, PVD-coated grades are the prime choice. They deliver tough yet sharp edges so they are great for handling adhesive materials. Moreover, they offer superior performance when it comes to finishing operations and center cutting drills.
- Determine size and shape of your desired cut: Different milling cutters are designed to produce different types of shapes, sizes and depths.
The diameter of a milling tool is an important factor when machining a part. A large diameter tool can quickly remove material and meet the overall geometry requirements of the finished part. However, there may be limitations depending on the specific features of a part. For instance, if there are necessary inside radii that need to be produced, an appropriately sized tool must be used to achieve this result. To speed up machining times, sometimes it is advisable to start with a large tool for removing bulk material, and then use a smaller one for completing finer details such as inner corners.
- Select the number of flutes based on your needs: More flutes can generate smoother finishes while fewer flutes provide faster cuts.
Milling flutes are channels cut into the bit of a milling cutter. The more flutes in the cutter, the higher the feed rate is, since less material is removed. This has a downside of reducing space available for swarf ejected from the cut and increasing the overall diameter of the milling cutter.
Conclusion:
Choosing the right milling cutter for your project can seem daunting. However, we are here to address this issue by introducing the different types of milling cutters and providing 4 steps you need to follow in order to choose the best milling tool for your project. With the right type and size of milling cutter, you can increase productivity while creating high-precision parts that would be difficult with traditional machining methods.
Are you unsure which milling cutters to choose for your project? Let us help. Leave a comment or contact us to discuss this further and get expert advice.
Leave a Comment