Drilling, boring, and reaming are all machining processes that involve cutting holes in metals or other materials. Each process has its uses and all are valuable when fabricating parts.
Understanding the difference between drilling, boring and reaming can be difficult for anyone new to the field of metalworking. This press release explains how each process works and what makes them unique. Let's dive in and understand the unique characteristics of each method.
1. What is Drilling?
Drilling is a process that involves cutting into or making a hole in a material, such as metal, wood, plastic, or other materials. It can be done manually with hand tools or machine-controlled with power tools. Drilling is commonly used in construction, engineering and manufacturing to create precise holes for various applications.
It involves using a drill bit to cut through the material, with the drill bit being attached to a machine or device that rotates in order to create the hole. The speed and pressure of rotation can be adjusted depending on the material and how deep you want the hole. Once complete, drilling can be used for tasks such as fastening bolts or adding attachments.
There are different types of drilling that can be used, depending on the application. These main include centre drilling, deep hole drilling.
● Centre drilling requires a drill bit that is aligned with the centre of the hole and used to create holes on the axis of a shaft in order to hold it in place between two centers. In the past, these have been used for drilling holes on machining centers but have since been replaced by spot drills due to their simpler design.
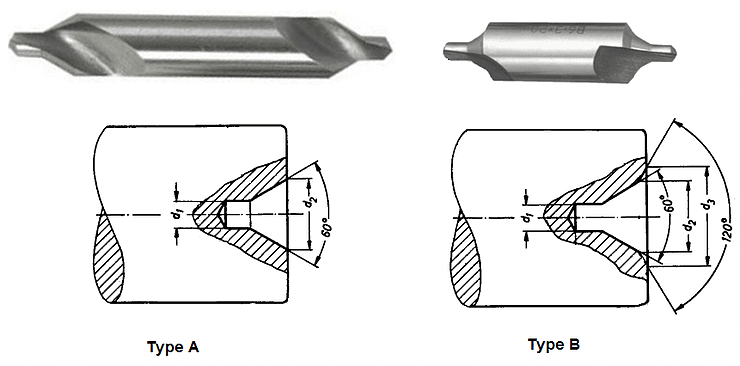
● Deep hole drilling requires a long drill bit and high-pressure lubricants. Which is a metal-cutting method used for creating new and further machining of existing bore holes. It enables precise, high-quality, and efficient manufacturing of components or parts with complex geometries.
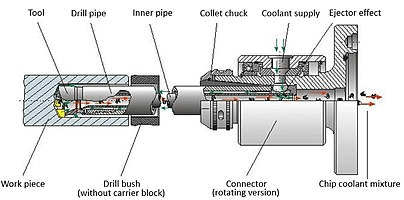
Each type of drill has its own advantages and disadvantages when it comes to creating holes so it is important to consider which one best suits your specific application.
2. What is Boring?
Boring is a process of increasing the diameter of an existing hole. It can be used to create precise and consistent holes in materials like metal, wood, and plastic. Boring is a great way to ensure accurate measurements when drilling or cutting as it allows for adjustable and predictable hole sizes. The end result is an even hole that meets your exact specifications.
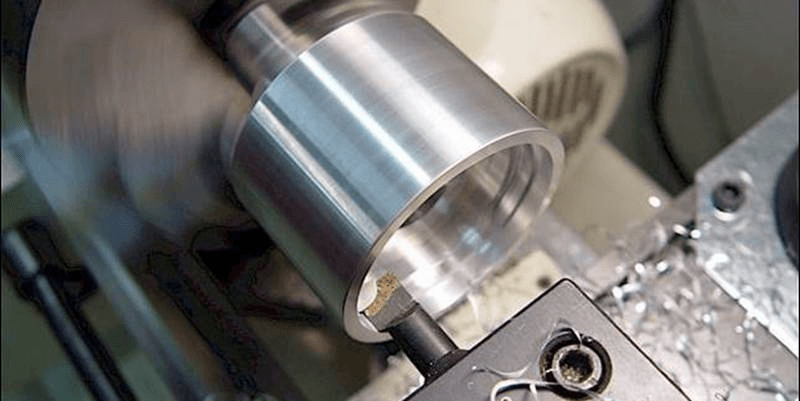
Boring is an essential part of metalworking and can be used for tasks like machining, welding, joining metal pieces together, and other applications. There are different types of boring such as line boring, back boring, trepanning (a form of drilling), counterboring (forming a counterbore or pocket), and pocket boring. Boring is a precise process that requires accurate measurements to ensure the desired size and shape of the hole.
● Line boring, or align boring, is an engine machining process used to create perfectly straight and aligned bores in the camshaft housing (saddles and tunnels) as well as the crankshaft. This specialized technique ensures high-precision alignment of all components.
● Back boring is a technique used in machining to create a hole with a shoulder that cannot be reached from the opposite direction. It can also help to improve the concentricity of the hole, as it is machined from only one position.
● Trepanning machining is a specialized deep hole drilling process that leaves the core material intact and ready for reuse. Different from gundrilling, trepanning machining uses a shorter, thicker cutting tool to cut metal which allows for greater depth-to-diameter ratios.
● Counterboring (forming a counterbore or pocket), Counterboring is a process that creates a cylindrical pocket with an enlarged diameter at the start of an already-drilled hole. This process helps to make room for inserts that have a larger diameter than the original hole.
3. What is Reaming?
Reaming is a technique used in machining that helps to create an accurate, smooth finish on the surface of a material. By using a reamer, rough edges can be removed and the internal diameter of the material can be precision finished. Reaming is often used on materials like steel, aluminum, and plastics to give them the perfect shape and size needed for any given project.
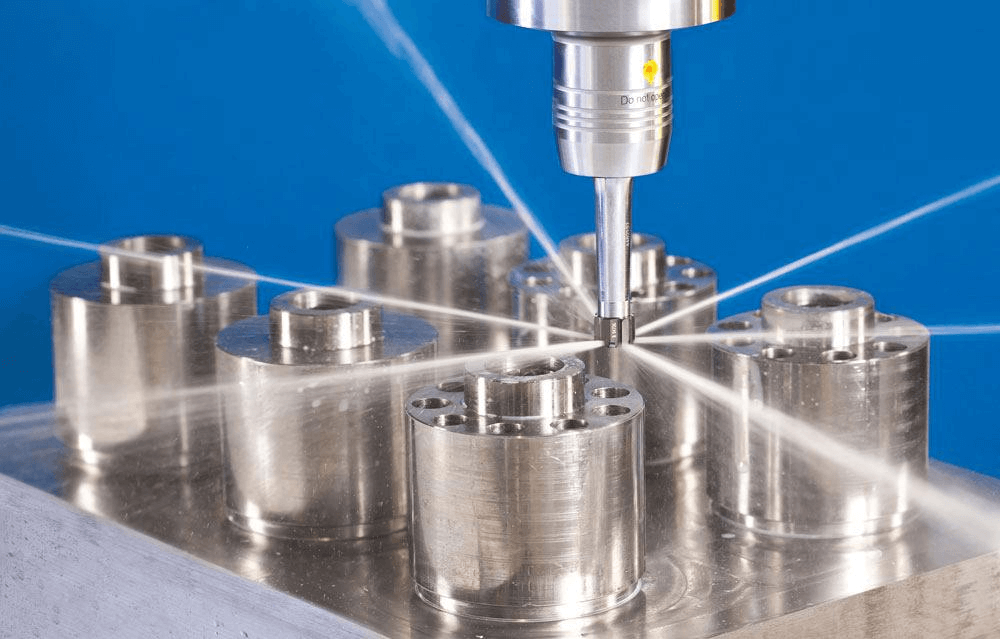
Reaming produces holes that are much more precise than those made with drill bits or other cutting tools. There are various types of reaming, including Hand Reaming, Straight reaming, Shell reaming, and others. Each type has its own specific uses and can be used to produce the desired result depending on the application.
● Hand reaming is the process of using a rotating cutting tool to create a precise hole in material. It is a quick and cost-effective way to finish holes that have been drilled or milled. Hand reaming can be used for both production and repair applications. Hand Reamers are tools that can be used to ream and enlarge holes in a variety of materials. They come in two varieties, rose or fluted reamers, which have a small taper on the cutting end for easy entry. Hand Reamers can be solid or extensible, but the enlargement is limited to a specific level. Additionally, the blades around its body are irregularly placed so that it reduces chatter when it's being used.
● Floating reamers are a type of reaming tool that are used to correct misaligned holes in rotary workpieces. They feature two replaceable and adjustable cutting edges that fit into one slot, allowing them to float in the radial direction. This makes floating reamers ideal for correcting issues on turret lathes.● Floating reamers are a type of reaming tool that are used to correct misaligned holes in rotary workpieces. They feature two replaceable and adjustable cutting edges that fit into one slot, allowing them to float in the radial direction. This makes floating reamers ideal for correcting issues on turret lathes.
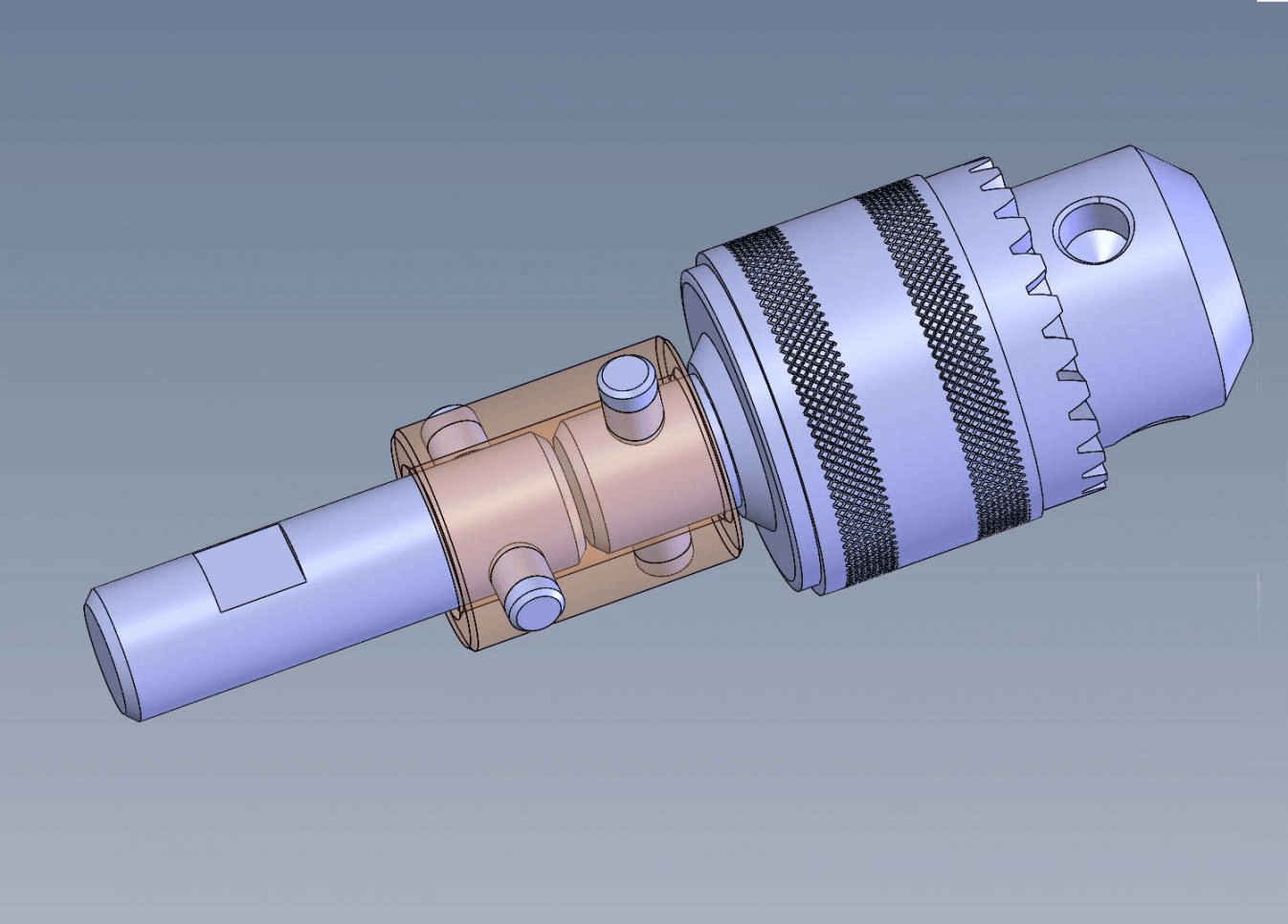
● Shell reamer arbors and shell reamers combine to create precise and accurate holes in a wide variety of materials. The arbors are designed to hold the reamer, or cutting tool, securely in place, giving it the best possible fit. These tools are specially engineered to free-cut materials and produce cleanly finished holes at the preferred size.● Shell reamer arbors and shell reamers combine to create precise and accurate holes in a wide variety of materials. The arbors are designed to hold the reamer, or cutting tool, securely in place, giving it the best possible fit. These tools are specially engineered to free-cut materials and produce cleanly finished holes at the preferred size.
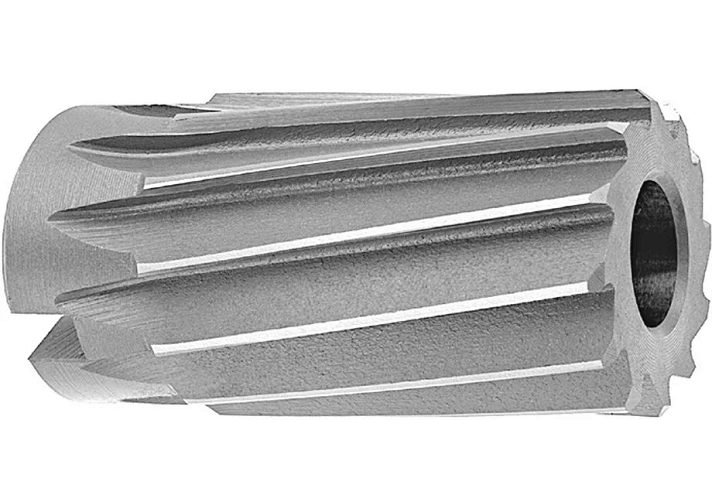
● Carbide reaming offer increased resistance to abrasion, allowing them to last longer and create smoother finished holes than traditional reamers. The solid carbide construction ensures that the reamer maintains a consistent surface finish and shape along its entire length, eliminating the need for costly corrections or refittings
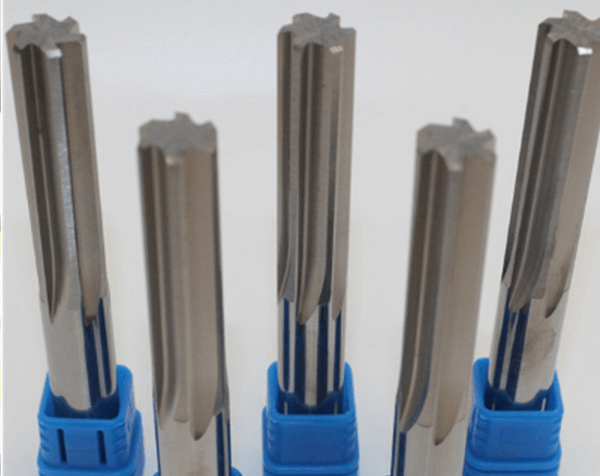
4. Drilling vs boring vs reaming, How do these processes differ from one another?
Drilling, boring, and reaming are all machining processes that involve cutting away material from a workpiece. However, they each have distinct differences. We have summarized these characteristics in the following chart to help you better understand them.
Machining process | Drilling | Boring | Reaming |
Purpose | Drilling originates a hole. | Boring enlarge the existing hole. | Reaming finishes hole surfaces. |
Tool Used | The cutting tool is called a drill, which is is a double point tool. | The cutting tool is called a boring bar, which is is a single point tool. | The cutting tool is called a reamer, which is a multi-point tool with a minimum of four cutting edges. |
Variations | Increase the length of the hole but not the diameter, as diameter is dependent on the drill tool. | Increase the diameter of the hole but not the length. A cylindrical hole can be tapered, but its length cannot be changed. | Both the diameter and length of the hole cannot be varied. |
Surface Quality | The quality of the surface is not very good. | The quality of the surface is better than drilling. | A highly finished surface can be observed. |
Requirements | Drilling requires accuracy for centering to be successful. | Boring requires a pre-existing hole which is created by drilling. | Reaming requires an existing hole that is the same size as the reamer's diameter. |
Phase of Fabriation | It is the first phase of fabrication. | It is the second phase of fabrication. | It is the third phase of fabrication and the finishing phase of the process. |
Material Removal Rate | The material removal rate is very high. | The material removal rate is less when compared to drilling. | The material removal rate is significantly less. |
Features | Drilling. The material removal rate is significantly less. The different types of drilling are Spot drilling, Centre drilling, Deep hole drilling, etc. | The different types of boring are: Line boring, Back boring, etc. | The different types of reaming are Straight reamer, Rose reamer, Shell reamer, etc |
Drilling, boring, and reaming are all processes used for cutting and enlarging the diameter of a hole in metal. Each of these processes has its own set of advantages and disadvantages that must be taken into consideration when selecting the best option for your application.
Machining process | Advantages | Disadvantages |
Drilling | - Precise: Achieve accurate results quickly and easily with high precision.
- Versatile: Different sizes of drill bits are available for a variety of materials.
- Efficient: Get the job done quickly and accurately with minimal labor required.
- Stable: With the workpiece held stationary, you can be sure that the drilling process is secure. | - Coordinate measuring machines (CMMs) are a bit pricey.
- If there is an issue with the process, it can be difficult to reset the whole system.
- It is impossible to create perfect holes exclusively through drilling alone.
|
Boring | - Increased efficiency: Get more done in a shorter time with boring machines.
- Cost-effective: An excellent investment for any factory, the machines have a longer lifetime.
- Low noise pollution: Noise levels are significantly reduced when using boring machines. | Boring is a process used to obtain samples. However, the operation can be time-consuming and difficult, which is its main disadvantage. |
Reaming | - Increased Efficiency: Automated reaming process ensures consistent results with less effort.
- Versatile Tool: One tool can be used for multiple operations and is suitable for different materials.
- Time Savings: Save time by streamlining the entire reaming process. | Reaming is not as precise as boring when it comes to hole size and location accuracy. Reaming can also lead to oversized holes, and the finished product may not be up to the desired standard. |
Conclusion:
Drilling, boring, and reaming are all metalworking processes that use cutting tools to create holes in metal materials. Each of these processes has its own unique purpose and uses depending on the desired outcome of the project. Understanding the differences between them can be beneficial in determining when to use which tool in a particular project.
Are you unsure which one is more suitable for your project? Let us help. Leave a comment or
contact us to discuss this further and get expert advice.
Leave a Comment